The Power of Plastic Injection Molding: Transforming Industries
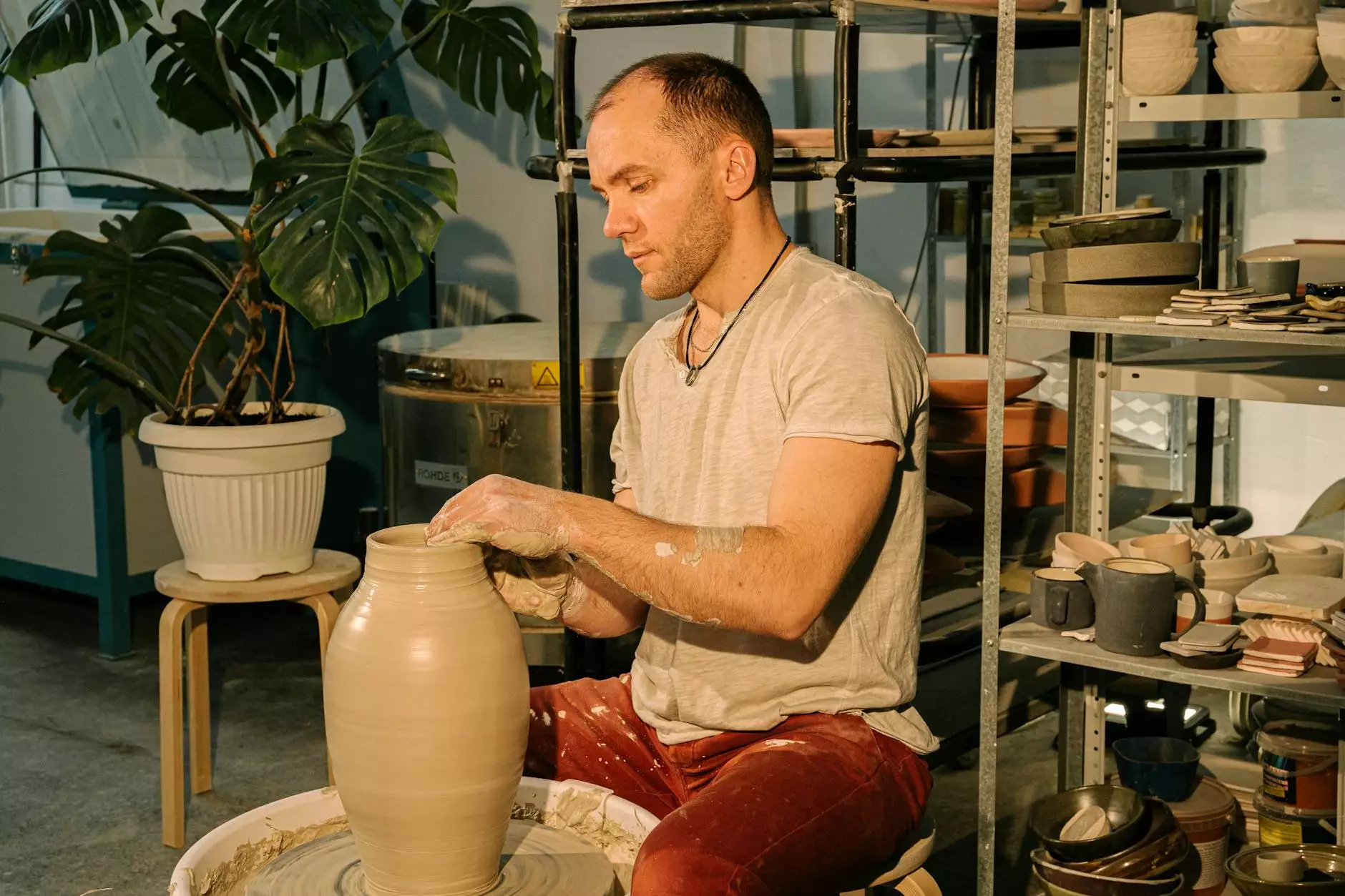
In today’s competitive market, businesses in various sectors are continually seeking ways to improve their manufacturing processes, reduce costs, and increase overall product quality. One of the most effective solutions available is plastic injection molding—a technique that has been widely adopted for its efficiency and versatility.
Understanding Plastic Injection Molding
Plastic injection molding is a manufacturing process used to create parts by injecting molten material into a mold. This method is particularly popular in industries ranging from automotive to consumer goods, as it allows for the production of complex shapes with high precision and minimal waste.
How It Works
The process begins with the heating of plastic granules until they melt. This molten plastic is then injected into a precisely designed mold where it cools and solidifies. Once cooled, the mold opens, and the finished component is ejected. This process enables businesses to produce high-quality components in large volumes efficiently.
The Benefits of Choosing a Plastic Injection Molding Company
There are numerous advantages to partnering with a dedicated plastic injection molding company. These benefits include:
- Cost Efficiency: By enabling mass production, injection molding reduces the cost per unit, which is crucial for maintaining competitive pricing.
- High Precision and Quality: Advanced technology used in injection molding ensures that every part produced meets strict design specifications.
- Versatility: A wide variety of materials can be used, allowing for customized solutions that cater to specific industry needs.
- Reduced Waste: The process minimizes raw material waste, making it an environmentally friendly option.
- Fast Production Time: Short cycle times facilitate the rapid production of large quantities of parts.
Exploring Metal Fabrication through Plastic Injection Molding
While the focus here is on plastic injection molding, it’s vital to recognize its intersection with metal fabrication. Within the realm of metal fabrication, incorporating plastic injection molding can lead to innovative product designs that blend both materials. For instance, creating hybrid components that utilize both plastic and metal can leverage the strengths of each material.
Applications in Metal Fabrication
There are multiple applications of plastic injection molding in the field of metal fabrication, including:
- Protective Covers: Use of molded plastic covers can protect sensitive metal components from environmental damage.
- Supporting Structures: Molded plastic components can serve as lightweight supports or housings for metal parts.
- Custom Connectors: Injection molding allows for the creation of intricate connectors that can join metal parts securely.
The Role of Deep Mould in the Plastic Injection Molding Industry
At Deep Mould, we pride ourselves on our expertise as a leading plastic injection molding company. Our commitment to quality, innovation, and customer satisfaction sets us apart in the industry. We leverage the latest technology and techniques to deliver outstanding products that meet our clients' diverse needs.
State-of-the-Art Technology
Our facility is equipped with cutting-edge machinery that ensures precision and efficiency in plastic injection molding. This investment in technology not only improves the quality of our products but also enhances our production capabilities, allowing us to fulfill large orders quickly and effectively.
Customized Solutions for Every Industry
We understand that each client has unique requirements. Our team at Deep Mould works closely with businesses to develop customized solutions that align with specific goals. From design consultations to prototype development, we are dedicated to turning your ideas into reality.
Choosing the Right Plastic Injection Molding Partner
Selecting a plastic injection molding company is a critical decision that can significantly affect your business's success. Consider the following key factors when making your choice:
- Experience and Expertise: Assess the company's track record and industry experience to ensure they are qualified to meet your needs.
- Quality Assurance: Look for companies that adhere to strict quality control measures and possess relevant certifications.
- Technology and Equipment: Ensure they utilize the latest technology and equipment for efficient production.
- Customer Support: Choose a company that values communication and provides robust customer support throughout the process.
- Flexibility: A good partner should be able to adapt to changing project requirements and deadlines.
Industry Trends in Plastic Injection Molding
As the industry evolves, several emerging trends are shaping the future of plastic injection molding. These trends include:
- Increased Use of Biodegradable Plastics: There is a growing demand for environmentally friendly materials which can be injected molded.
- Emphasis on Sustainability: Companies are increasingly focusing on sustainable practices to reduce environmental impact.
- Smart Manufacturing: The integration of IoT and automation is enabling smarter, more efficient production processes.
- Customization and Personalization: Customers expect tailored solutions that cater to their specific needs and preferences.
- Advancements in 3D Printing: The growth of 3D printing technology is leading to new possibilities in mold design and prototyping.
Conclusion
In summary, the benefits of collaborating with a proficient plastic injection molding company like Deep Mould are extensive. From enhancing product quality to reducing production costs, our expertise in injection molding can dramatically improve your manufacturing process. As industries continue to evolve, it is crucial to stay ahead of the trends and embrace innovative solutions that will propel your business towards success. If you are looking to refine your production capabilities, consider partnering with Deep Mould for all your plastic injection molding needs.