Fitting and Lubrication: A Comprehensive Guide to Optimal Performance
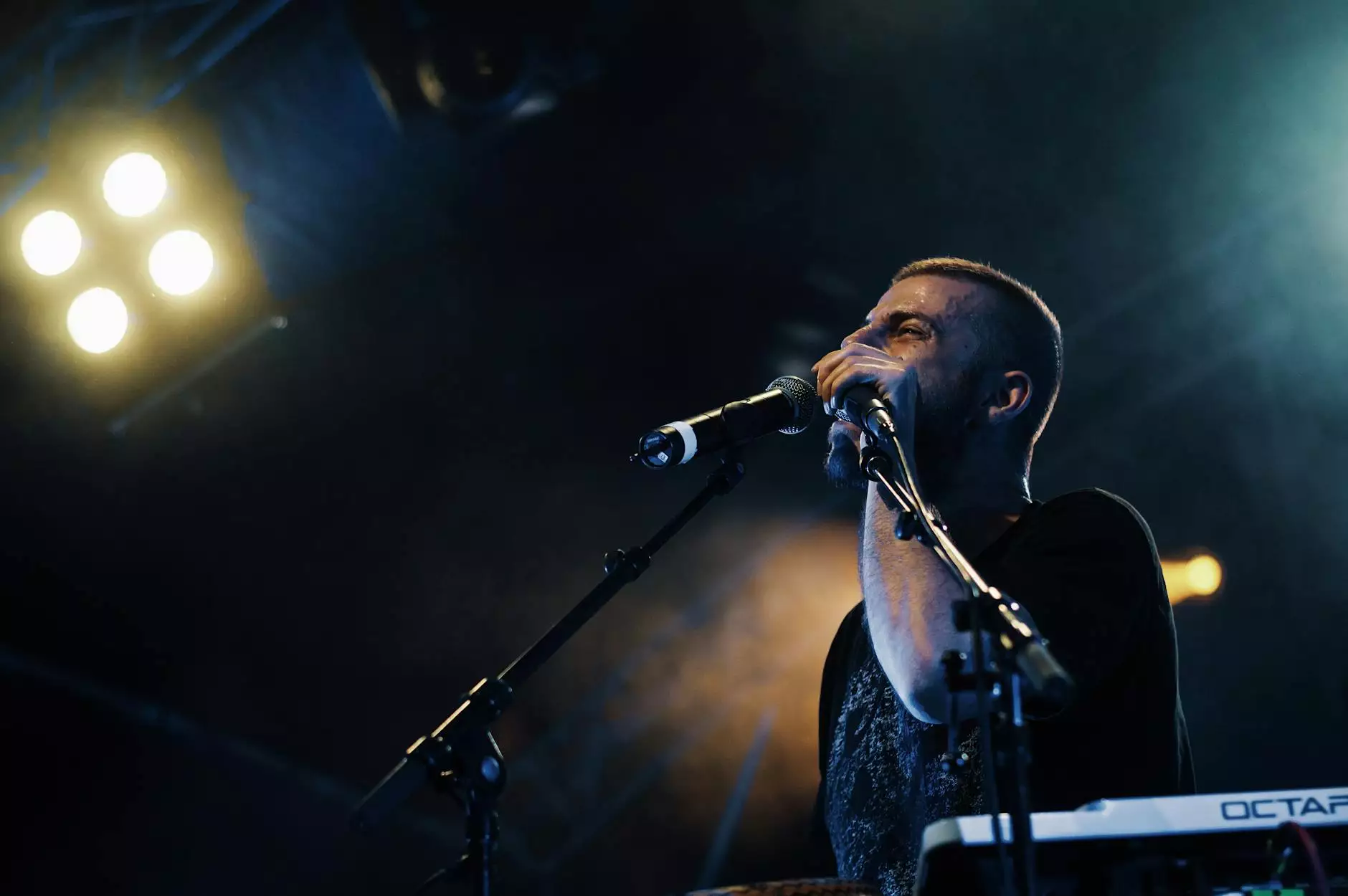
In the world of mechanical systems, combining high-quality fittings with appropriate lubrication techniques is pivotal for ensuring optimal performance and longevity. This article delves deep into the significance of fittings and lubrication, offering valuable insights for businesses and professionals involved in various industries.
Understanding Fittings
Fittings play a crucial role in connecting multiple components within mechanical systems. They are designed to facilitate the flow of fluids or gases, ensuring a tight and secure connection that can withstand pressure and environmental conditions.
Types of Fittings
- Elbow Fittings: Used to change the direction of flow.
- Tee Fittings: Allow branching off from a main line.
- Reducer Fittings: Enable the transition from a larger pipe to a smaller one.
- Cap Fittings: Seal the end of a pipe or fitting.
- Union Fittings: Facilitate easy disconnection of piping without needing to cut.
Importance of Quality Fittings
Investing in quality fittings is essential for ensuring performance and reliability. Poor-quality fittings can lead to leaks, pressure losses, and failures, which can be costly in terms of repairs and downtime. High-grade fittings are manufactured to exacting standards to endure the rigors of operation, thus safeguarding your equipment and ensuring a smooth workflow.
Key Features to Look For
When considering fittings, there are various characteristics that should not be overlooked:
- Material: Common materials include brass, stainless steel, and plastic, each with its specific applications.
- Pressure Ratings: Ensure the fitting can handle the operational pressure.
- Temperature Resistance: Evaluate the fitting’s performance under various temperature conditions.
- Compatibility: Ensure the fitting is compatible with the fluid or gas being transported.
The Role of Lubrication
Lubrication is vital for reducing friction and wear between moving parts in machinery. It helps maintain the efficiency of mechanical operations while prolonging the lifespan of components. Proper lubrication systems must be employed to ensure a steady flow of lubricant to all necessary points within a mechanical system.
Types of Lubricants
There are several types of lubricants that serve various purposes:
- Oil: Commonly used for its ability to provide necessary cooling and protection against corrosion.
- Grease: Thickened oil that offers protection in locations where oil might be too fluid.
- Solid Lubricants: Such as graphite or molybdenum disulfide, which reduce friction in extreme conditions.
- Synthetic Lubricants: Engineered for superior performance under high-stress conditions.
Benefits of Proper Lubrication
Employing effective lubrication techniques yields numerous benefits, such as:
- Reduced Friction: Minimizing friction prolongs component life.
- Enhanced Performance: Well-lubricated systems operate more smoothly and efficiently.
- Corrosion Prevention: Lubricants can form a protective film that minimizes corrosion risks.
- Energy Efficiency: Lower friction means less energy consumption, saving costs in the long run.
Integrating Fittings and Lubrication Systems
The synergy between fittings and lubrication systems is vital for mechanical efficiency. Proper selection of fittings helps ensure that lubricants reach all moving parts effectively. Here are best practices for integration:
- Choose Fittings Wisely: Select fittings that support the specific lubricant used.
- Adequate Delivery System: Ensure that the lubrication system delivers the right amount of lubricant to keep fittings and components operational.
- Regular Maintenance: Establish a routine checkup to identify any leaks or breakages in fittings or lubrication pathways.
- Monitor System Performance: Keep track of how fittings and lubricants are performing together, adjusting as necessary to maintain efficiency.
Best Practices for Maintenance
To ensure both fittings and lubrication systems work harmoniously, follow these maintenance best practices:
- Conduct Regular Inspections: Look for signs of wear, leaks, or damage frequently.
- Clean Fittings: Regularly clean fittings to prevent buildup that can affect performance.
- Change Lubricants: Ensure that lubricants are changed at recommended intervals to maintain optimal performance.
- Keep Records: Document maintenance activities to track performance and spot patterns that require attention.
Conclusion
In conclusion, understanding the integration of fittings and lubrication is vital for any business that relies on mechanical systems. By prioritizing quality fittings and proper lubrication practices, companies can enhance efficiency, reduce downtime, and extend the life of their equipment. Implementing these practices not only ensures safety and reliability but also contributes to overall operational cost savings.
Explore our range of high-quality fittings for sale at fitsch.cn and discover how we can assist you in achieving optimal performance for your mechanical systems.
fitting, lubrication