Understanding Pressure Die Casting Machine Manufacturers
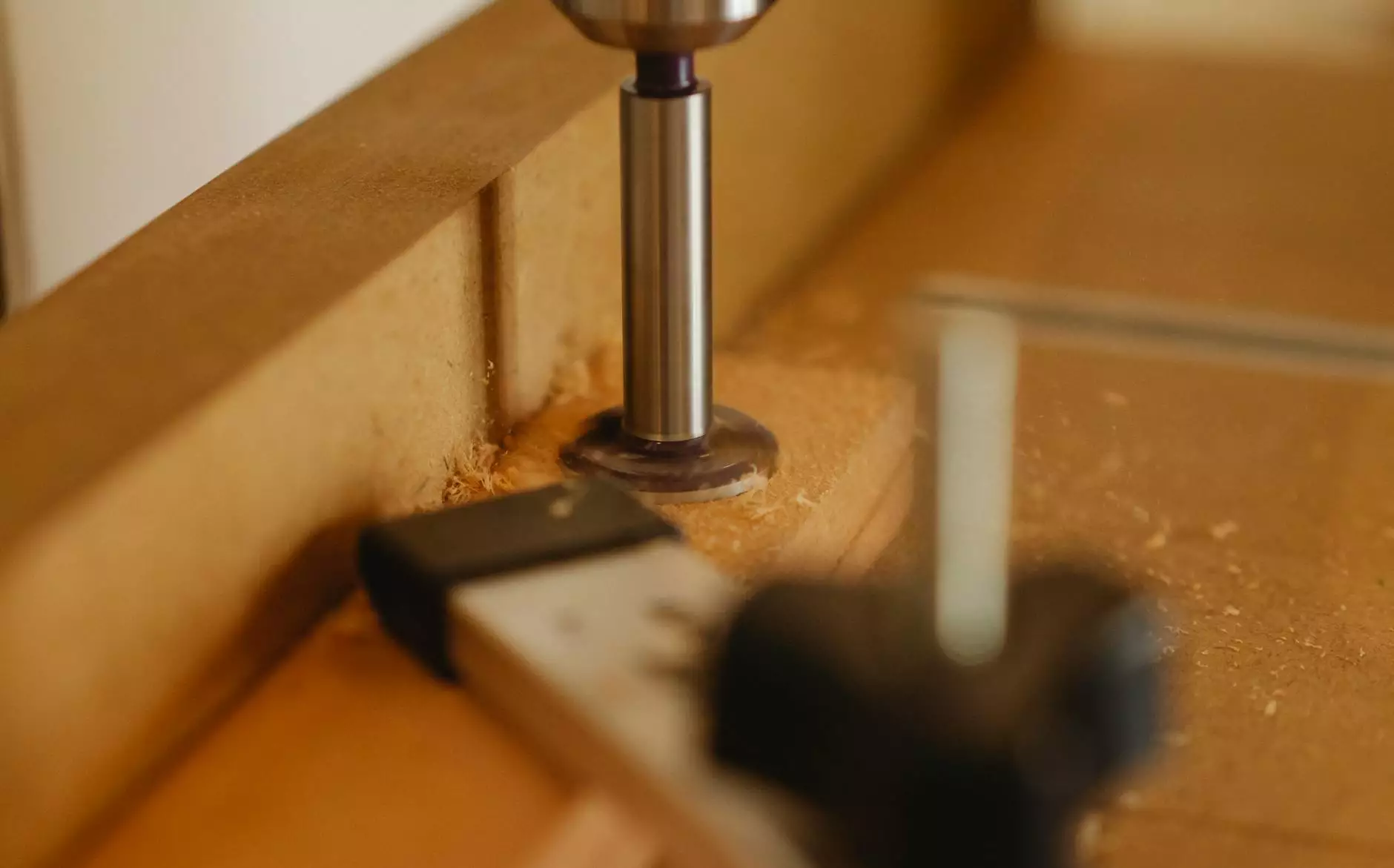
In today's industrial landscape, pressure die casting machine manufacturers play a crucial role in the production of high-quality metal components. With advancements in technology and shifting market demands, these manufacturers have evolved significantly to meet the needs of various sectors, including automotive, aerospace, and electronics. This comprehensive guide delves into the intricacies of the pressure die casting process, the characteristics of effective manufacturers, and the essential factors to consider when choosing a supplier.
What is Pressure Die Casting?
Pressure die casting is a manufacturing process that involves injecting molten metal into a mold under high pressure. This method is particularly effective for producing complex shapes with close tolerances. The process is characterized by its ability to generate large volumes of parts with superior surface finishes and minimal machining requirements.
Key Benefits of Pressure Die Casting
- High Precision: The pressure die casting method allows for precise reproduction of intricate designs and detailed features.
- Efficient Production: With rapid cycle times, manufacturers can produce high volumes of parts quickly, enhancing overall productivity.
- Material Versatility: Although primarily used with non-ferrous alloys like aluminum, magnesium, and zinc, pressure die casting can also accommodate other materials.
- Excellent Surface Finish: Parts produced through this method typically require minimal post-processing due to their smooth finishes.
- Reduced Waste: The process generates less scrap compared to traditional casting methods, making it more cost-effective.
The Role of Pressure Die Casting Machine Manufacturers
Pressure die casting machine manufacturers are at the forefront of producing the equipment that enables this innovative manufacturing technique. These companies provide the machinery needed for both low-pressure and high-pressure die casting, each suited to different production needs.
Characteristics of Leading Manufacturers
When evaluating pressure die casting machine manufacturers, it is essential to consider several characteristics that distinguish the best in the industry:
- Innovation: The best manufacturers continually invest in research and development to innovate their machinery, integrating the latest technologies such as automation and artificial intelligence.
- Quality Assurance: Top manufacturers adhere to stringent quality standards, ensuring that their machines are durable, efficient, and capable of producing high-quality parts.
- Customer Support: Excellent manufacturers provide ongoing support, training, and maintenance services to ensure the optimal operation of their machines.
- Customization: Leading manufacturers offer customizable solutions tailored to the specific needs of their clients, addressing unique production challenges.
- After-Sales Service: Comprehensive after-sales service is a hallmark of a reputable manufacturer, ensuring that clients can maintain peak operational performance.
Choosing the Right Pressure Die Casting Machine Manufacturer
Selecting the right pressure die casting machine manufacturer can significantly impact your production capabilities. Here are several factors to consider:
1. Industry Experience
Look for manufacturers with a proven track record in the industry. Experienced manufacturers are more likely to understand the complexities involved in die casting and can provide machines that effectively meet your needs.
2. Technology and Equipment
Evaluate the technology used in the manufacturing process of the machines. Modern machinery should incorporate advanced automation features, ensuring efficiency and precision.
3. Customer Testimonials and Case Studies
Research customer testimonials and case studies to gauge the satisfaction levels of other clients. Understanding how a manufacturer has helped similar businesses can provide valuable insights.
4. Compliance and Certifications
Ensure that the manufacturer complies with industry standards and possesses relevant certifications, as this reflects their commitment to quality and safety.
5. Cost-Effectiveness
While price shouldn’t be the sole determining factor, it is essential to assess the cost-effectiveness of the machinery in relation to its capabilities and your production needs.
The Future of Pressure Die Casting
The future of pressure die casting is bright, with significant advancements on the horizon. As technology continues to evolve, we can expect innovations that enhance efficiency, sustainability, and product quality.
Impact of Automation
Automation is set to transform the die casting industry. The integration of robotics and smart technologies will streamline operations, reduce labor costs, and enhance precision in the manufacturing process.
Sustainable Practices
As industries shift towards sustainability, pressure die casting manufacturers are adopting greener practices. This includes recycling materials, reducing energy consumption, and implementing eco-friendly manufacturing processes.
Enhanced Materials
Research into new materials and alloys will also play a crucial role. Manufacturers are exploring innovative materials that not only reduce weight but also enhance performance in various applications.
Conclusion
In conclusion, the landscape of pressure die casting machine manufacturers is dynamic and continuously evolving. As businesses look to leverage the benefits of pressure die casting, it is imperative to choose a manufacturer that combines experience, innovation, and customer-centric practices. By understanding the essential aspects of the die casting process and the features of leading manufacturers, businesses can position themselves for success in an increasingly competitive market.
Visit deepmould.net for more information on metal fabrication services and to explore our offerings in pressure die casting technology.